Protein Packaging Upgrade
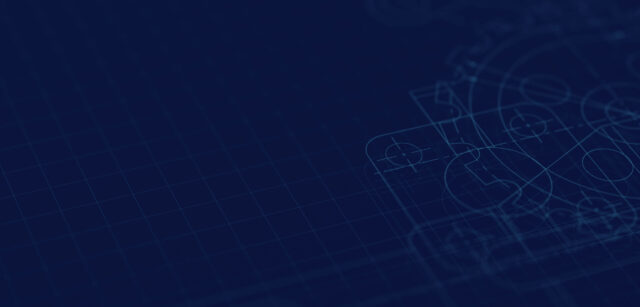
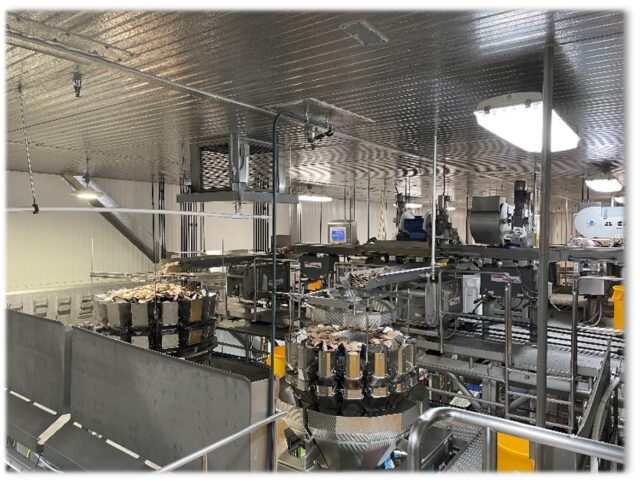
In 2022, Sharpe Engineering partnered with a leading protein producer to streamline operations across four packaging lines. The goal was to increase capacity, enhance flexibility, and improve overall efficiency, significantly boosting production output and operational agility.
This project exemplifies Sharpe Engineering’s ability to manage complex, multi-phase expansions with precision and adaptability. From initial scope development to installation and final commissioning, Sharpe delivered innovative engineering solutions that met the client’s immediate needs and prepared them for future success.
Problem
Packaging inefficiencies limited the client’s growth. Rising demand outpaced capacity, prompting a strategic overhaul to boost throughput and flexibility.
The client faced bottlenecks across multiple packaging lines, limiting throughput and reducing flexibility in directing frozen products to different lines. Additionally, aging equipment and sanitation processes required upgrading to meet increasing production demands and food safety standards.
Solution
Sharpe Engineering designed and installed a comprehensive packaging reconfiguration strategy, addressing key components across the packaging area.
Increased Transfer Efficiency
- Sharpe procured and installed a bucket, belt, and horizontal motion conveyors to optimize material flow, minimize product handling, and maximize delivery point flexibility.
Enhanced Weighing Accuracy
- Integrated radial combination scales for precise, high-speed weighing to support increased capacity.
Upgraded Packaging Systems
- Installed vertical form fill seal (VFFS) machines to ensure reliable, high-efficiency IQF (Individually Quick Frozen) sausage patty packaging.
Sanitation Improvements
- Upgraded platforms, wash walls, and drains to align with strict food safety regulations.
Results
The solutions increased capacity and streamlined processes, resulting in higher production rates, less downtime, and improved adaptability.
- Product Handled: IQF Sausage Patties
- Production Rate: 26,000 lbs per hour
- Packaging Format: Pillow and gusseted flexible bags
- Production Increase: 30% boost in output
- Operational Flexibility: Achieved seamless redirection of frozen products to any of the four packaging lines, reducing downtime and bottlenecks.
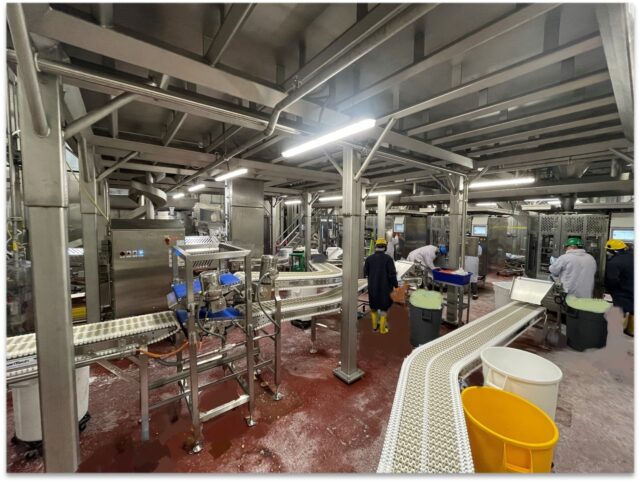
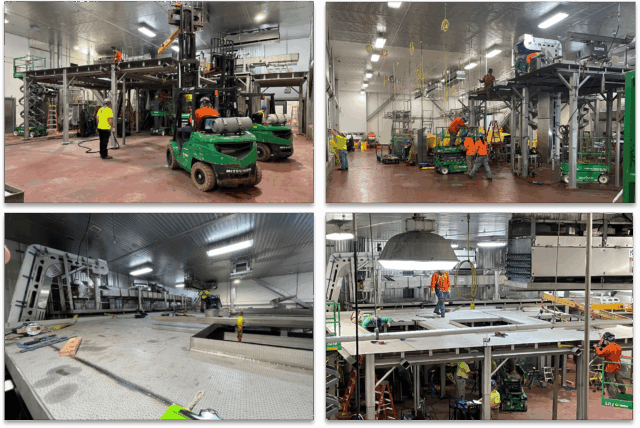
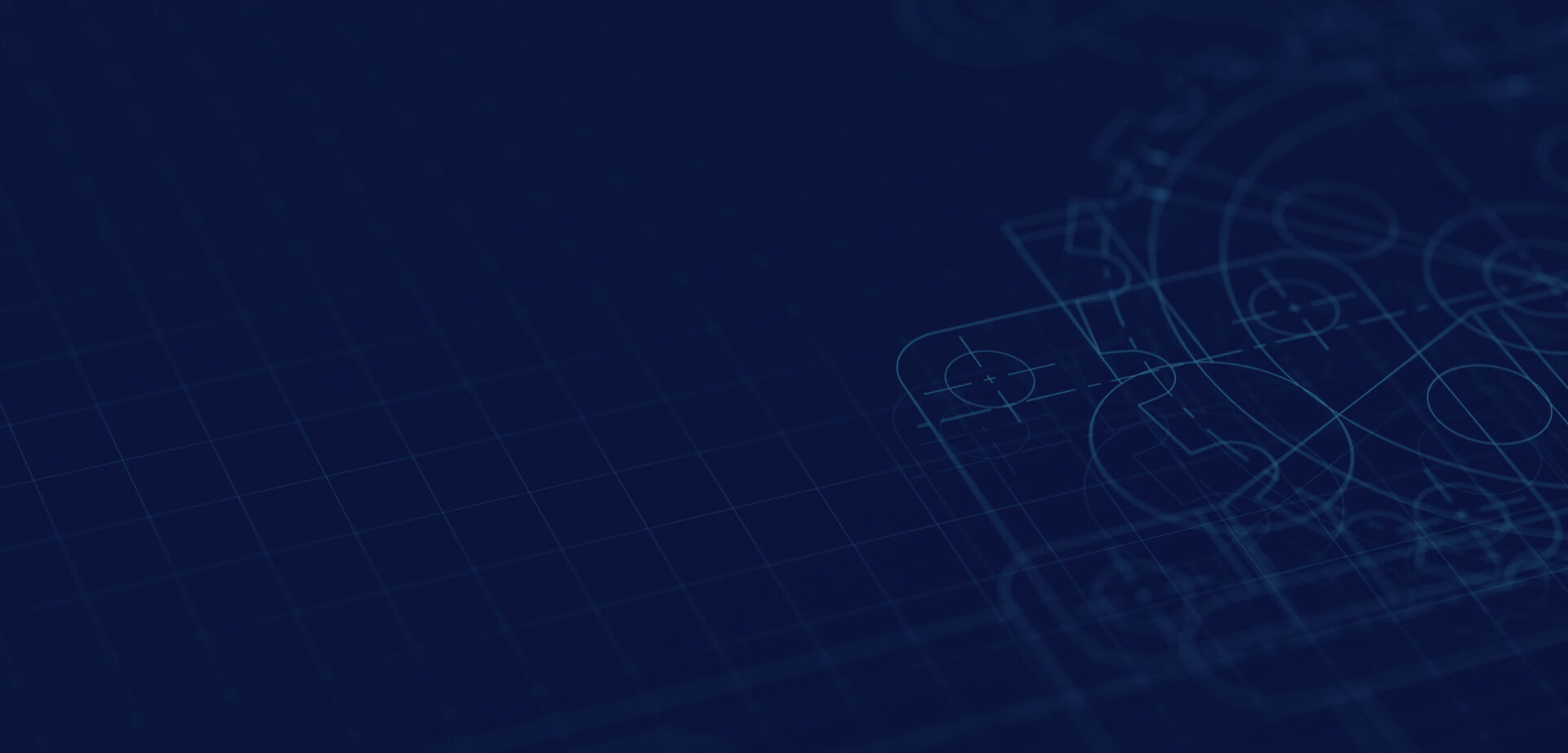
Ready to speak with our team of experts?
Feel free to give us a call, email, or fill out a short inquiry— let’s complete your project together.