IQF Skillet Meals
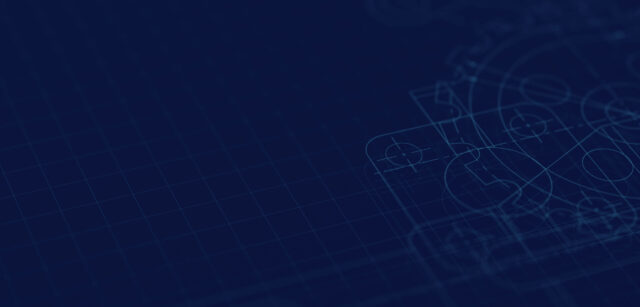
Sharpe Engineering supported the development and execution of a new IQF skillet meal production system at a food manufacturing facility in Texas. This comprehensive project included preliminary engineering, execution engineering, and mechanical installation supervision to ensure seamless delivery and operational success.
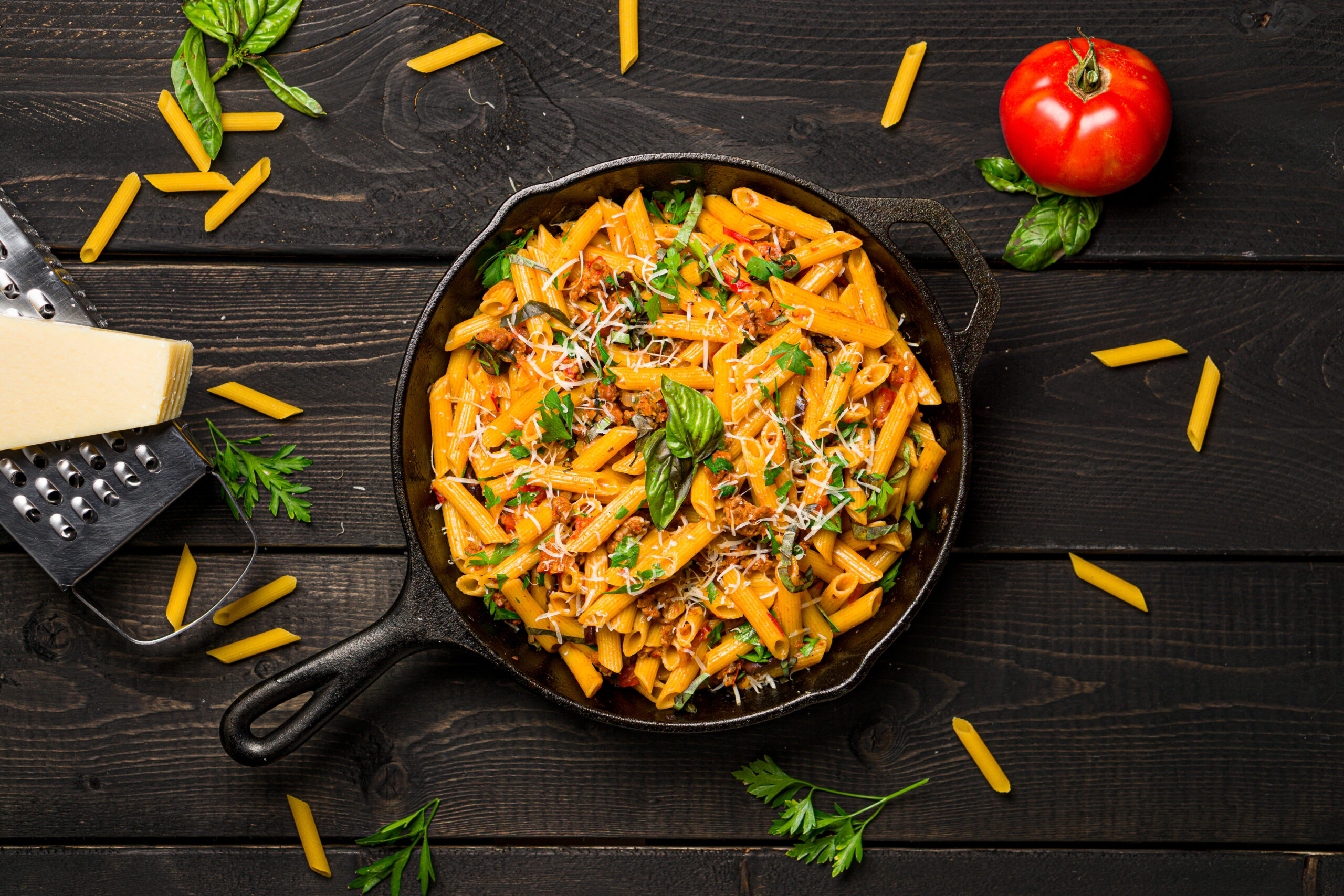
Problem
The client sought to enhance their production capabilities by integrating a new IQF skillet meal line into a new area of their existing facility. This required overcoming design complexities, ensuring alignment with industry safety and quality standards, and meeting tight deadlines to minimize downtime.
Sharpe Engineering played a critical role in addressing these challenges by providing front-end guidance and unbiased evaluation. The success of the project hinged on effectively managing several key factors.
- Timeline Management: Coordinating activities among multiple stakeholders to meet tight project deadlines and ensure timely delivery.
- Design Complexity: Integrating the new production line seamlessly into the facility’s existing infrastructure while addressing spatial and technical constraints.
- Operational Standards: Maintaining strict compliance with safety protocols and industry regulations throughout the design and installation process.
Solution
A thoroughly designed and engineered line achieved through collaboration between the client, Sharpe, and selected vendors.
Preliminary Engineering
- Conducted initial feasibility studies and developed preliminary layouts for the production system.
- Developed detailed layout designs tailored to the client’s facility and production goals.
Equipment Procurement
- Supplied critical components, including radial combination scales, transfer systems, and the secondary packaging system, integral to the new production line.
Execution Engineering
- Managed the entire project lifecycle including scheduling, vendor coordination, and procurement assistance.
- Integrated electrical controls ensuring seamless communication between all components of the production line.
- Delivered detailed final layout designs, engineering documentation, and equipment specifications.
Mechanical Installation Supervision
- Directed on-site installation activities over a 14-day period, collaborating with local crews and vendor technicians to ensure quality execution.
- Ensured adherence to safety protocols, quality benchmarks, and operational best practices.
Results
Sharpe Engineering successfully delivered a state-of-the-art IQF skillet meal production system, achieving all project objectives on time and within budget.
- Operational Excellence: The new system increased production capacity and streamlined workflows, enabling consistent and efficient output to meet growing demand.
- Seamless Integration: The production line was fully integrated into the existing facility, utilizing advanced engineering designs and precise installation practices to optimize space and processes.
- Optimal System Performance: The integration of radial combination scales, transfer systems, and secondary packaging equipment ensured the system operated with high accuracy and reliability.
- Compliance and Safety: All installations adhered to industry safety protocols and quality standards, minimizing risks and ensuring long-term operational stability.
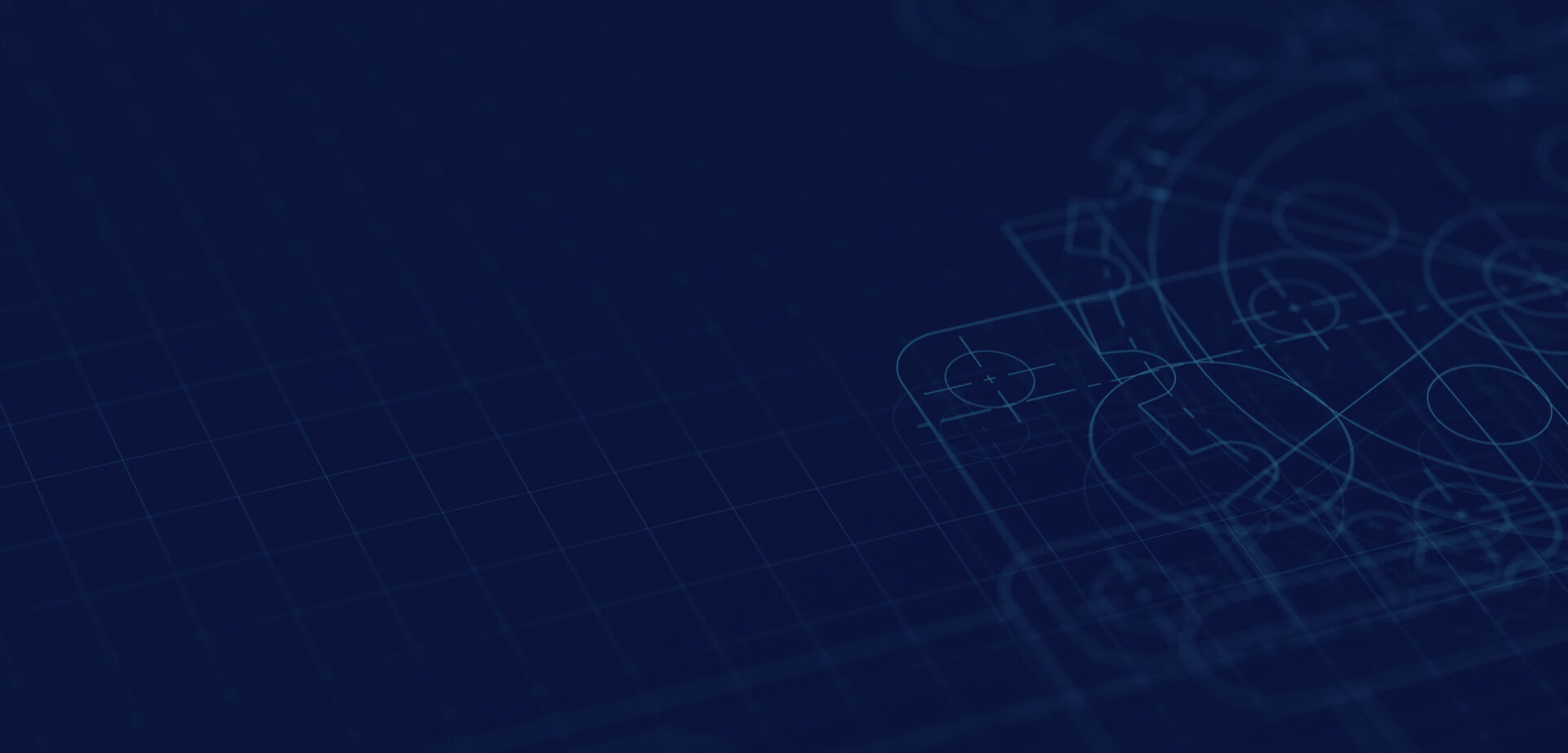
Ready to speak with our team of experts?
Feel free to give us a call, email, or fill out a short inquiry— let’s complete your project together.