Gummy Packaging
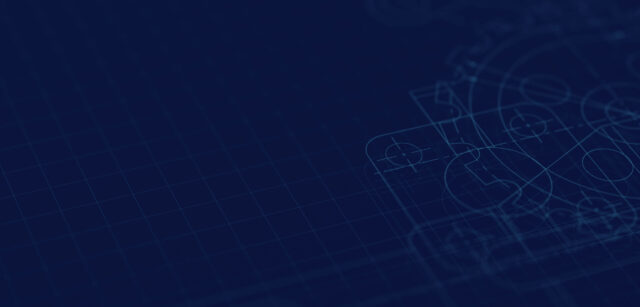
Sharpe Engineering partnered with a leading confectionery manufacturer to deliver a comprehensive packaging system for their new facility. This initiative involved the design, engineering, and installation of a state-of-the-art packaging line capable of handling high volumes of gummy production across two mogul lines. Sharpe Engineering’s ability to deliver customized, high-efficiency packaging systems highlights how we help clients expand capabilities and drive operational success.
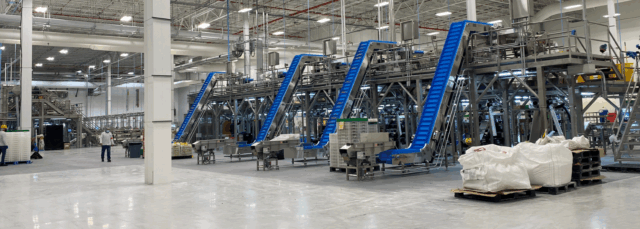
Problem
The manufacturer needed to scale production with an efficient packaging system that increased throughput while ensuring quality and compliance with strict quality standards.
The desire was for a fully integrated packaging system to meet growing production demands. The target was to establish two mogul lines capable of producing 10,000 and 12,000 pounds of gummies per hour, seamlessly integrated with packaging. The project faced logistical challenges due to import restrictions and late-stage equipment deliveries, which could delay production timelines.
Solution
Sharpe Engineering provided end-to-end project management, engineering design, procurement, and vendor coordination to ensure seamless execution.
- Conveyor Systems
- Custom stainless-steel conveyors for product transport, rejection, and rerouting.
- Polyurethane belts, pneumatic retract systems, and quick-release mechanisms to enhance efficiency.
- Transfer Shakers
- Precision shaker systems to manage gummy flow and feed into inspection lines.
- Tray Filler System
- Automated net weight tray filler for 30 lb bulk packaging with integrated vibratory feed and advanced PLC recipe control.
- Bagger and Scale Systems
- Integrated radial combination scales with vertical form fill seal baggers to optimize speed and accuracy.
- Managed vendors to ensure smooth integration and optimal performance.
- Metal Detection Systems
- Advanced metal detection systems to ensure product quality and safety.
- Scale Parts Washer
- Industrial-grade parts washer for scale components, ensuring sanitary compliance.
Controls and Automation
- Deployment of PLCs, HMIs, and VFDs for integrated, automated control.
- Operator stations and remote I/O enclosures for improved operational flexibility.
Results
The project contributed to a significant boost in production efficiency and operational reliability, reducing bottlenecks and ensuring consistent output.
- Commissioned and launched production lines that met or exceeded throughput targets.
- Reduced downtime and increased efficiency with automated handling, rejection, and packaging systems.
- Enhanced hygiene standards through dedicated scale parts washing equipment.
- Streamlined equipment import and installation, overcoming initial logistical challenges.
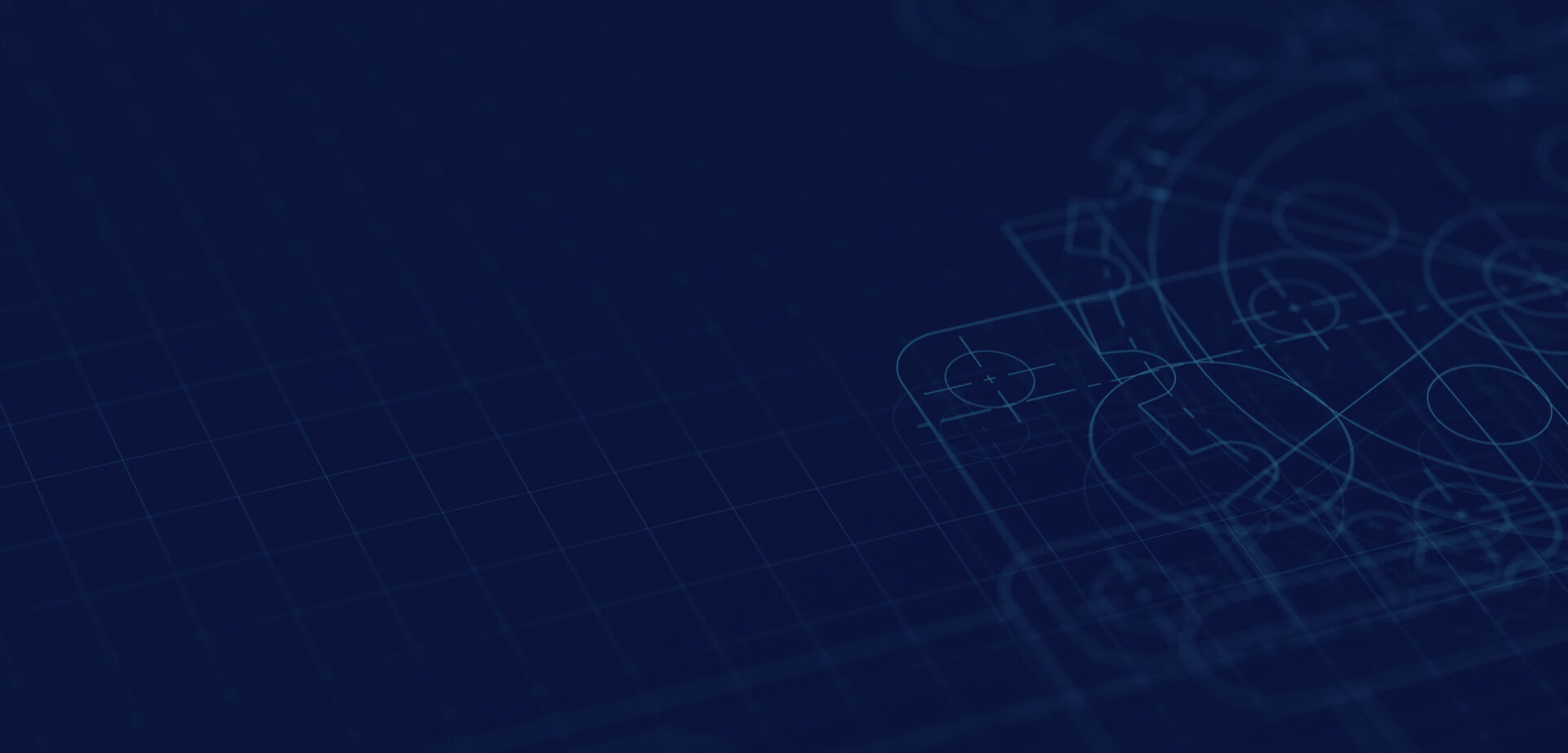
Ready to speak with our team of experts?
Feel free to give us a call, email, or fill out a short inquiry— let’s complete your project together.